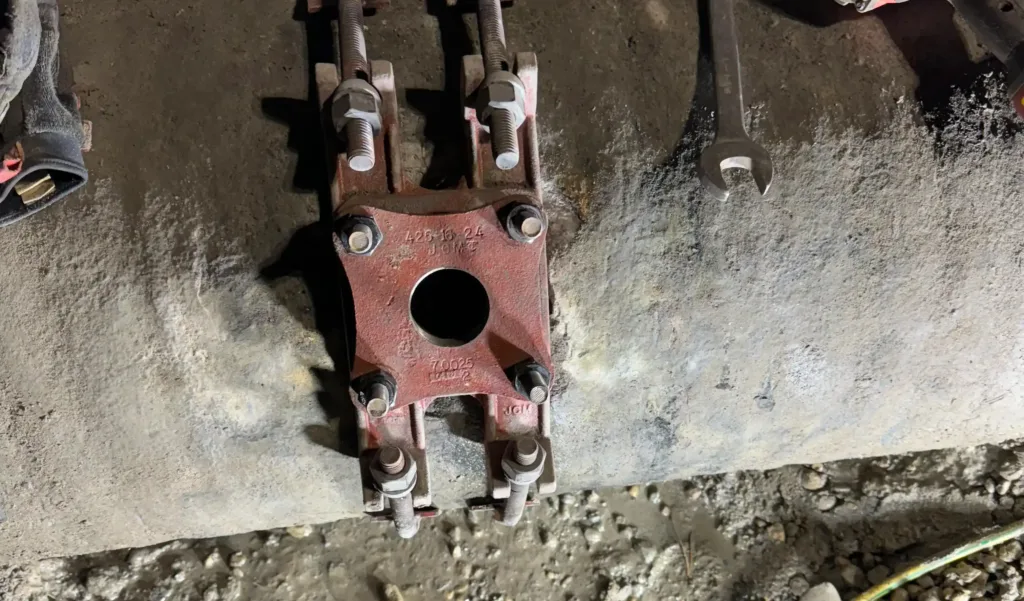
What is PCCP (Prestressed Concrete Cylinder Pipe)?
Prestressed Concrete Cylinder Pipe (PCCP) is an essential component of modern pipeline infrastructure, combining the tensile strength of steel with the compressive durability of concrete. Engineered to withstand high internal pressures and external loads, PCCP is widely used in municipal water services, wastewater management, and industrial applications. Its unique construction makes it the ideal solution for large-diameter pipelines that demand both strength and long-term performance.
History and Evolution of PCCP
Developed in the early 20th century, PCCP quickly gained traction due to its durability and capacity to handle high-pressure systems. By the 1960s, it became a standard in large-scale infrastructure projects, especially during periods of significant water infrastructure expansion. Over the decades, improvements in materials and manufacturing processes have enhanced PCCP’s strength and reliability, with industry standards like AWWA C301 and ASTM specifications guiding its continued development.
Types of PCCP
PCCP is primarily available in two forms, each designed for specific operational needs:
- Lined Cylinder Pipe (LCP): This design features a steel cylinder encased in a concrete core, with prestressing wires wrapped around the steel to reinforce internal pressure resistance and prevent corrosion. LCP is best suited for high-pressure applications and allows for easier inspection and maintenance.
- Embedded Cylinder Pipe (ECP): In this design, the steel cylinder is fully embedded within the concrete core, offering superior protection against external loads and environmental factors. ECP is ideal for underground installations where external pressure and corrosion are concerns.
These two types cater to varying demands, providing flexibility in design and installation based on environmental conditions and operational pressures.
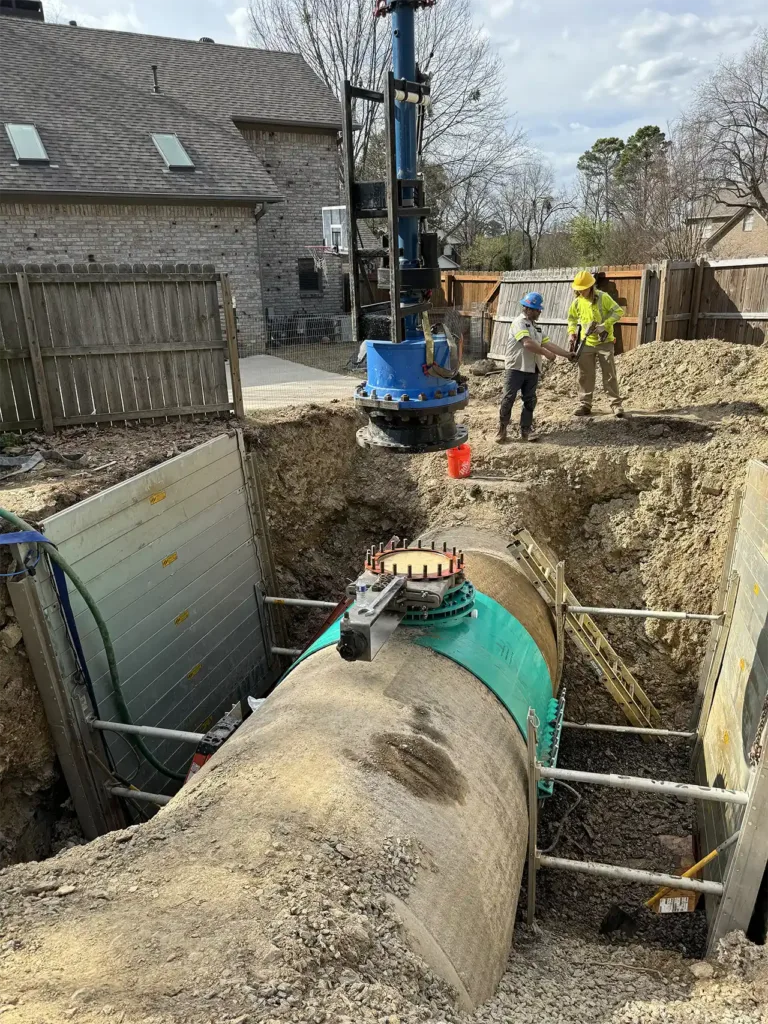
Manufacturing Process of PCCP
The construction of PCCP involves a precise and multi-step manufacturing process designed to ensure structural integrity and longevity. It begins with the formation of a robust concrete core that serves as the pipe’s foundation. A steel cylinder is then placed within or around this core, depending on the pipe type. High-tensile prestressing wire is helically wound around the cylinder to provide reinforcement. Finally, the pipe is coated with mortar or concrete to protect against corrosion and external damage. Each stage undergoes rigorous quality control testing to meet industry standards for strength and durability.
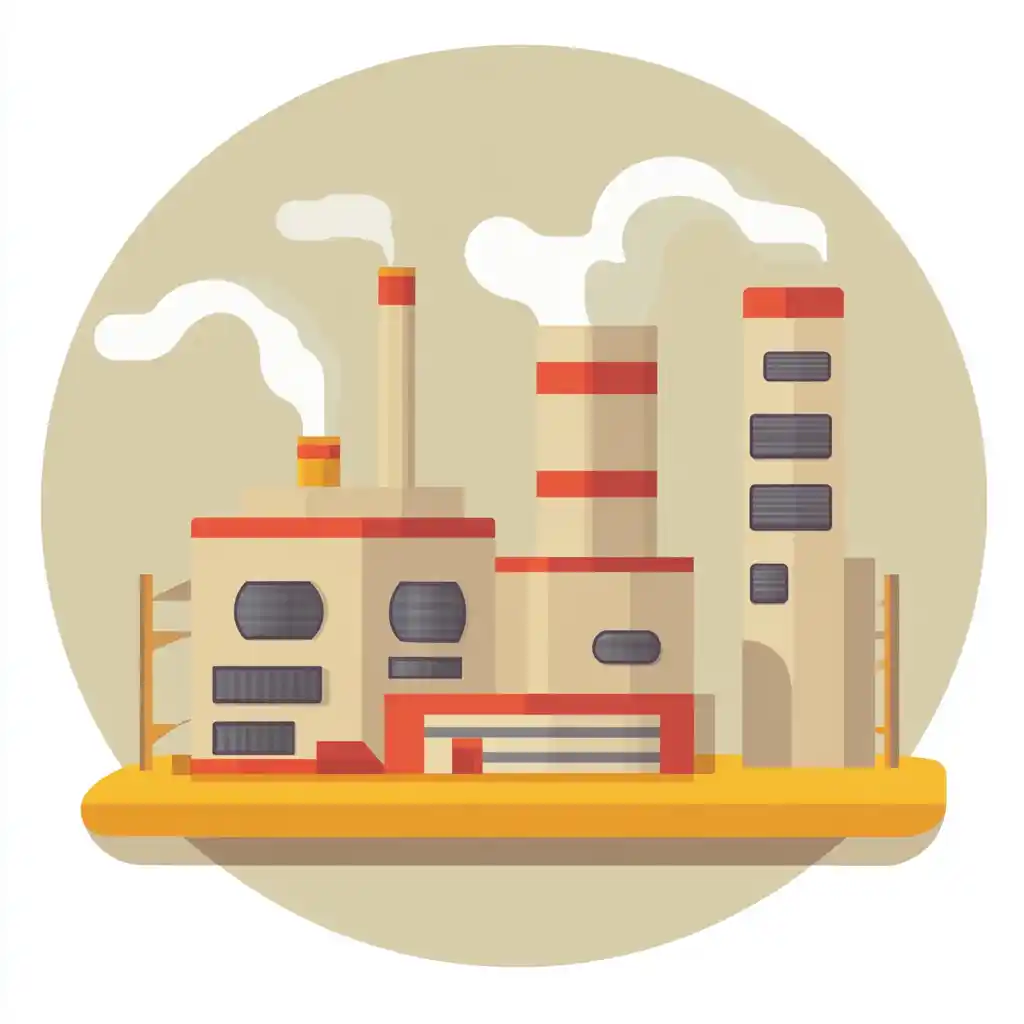
Applications of PCCP
PCCP is a versatile solution for a wide range of infrastructure projects, thanks to its ability to handle high pressures and large volumes. It is commonly used in:
- Municipal Water Transmission: PCCP is the backbone of large-scale water supply systems, ensuring consistent and reliable delivery of potable water.
- Wastewater Management: Its durability makes it ideal for sewer systems and stormwater drainage pipelines.
- Industrial Systems: Facilities with high water demands, such as power plants and manufacturing sites, rely on PCCP for cooling water and process pipelines.
- Agricultural Irrigation: PCCP supports high-capacity irrigation systems that require robust, long-lasting infrastructure.
- Power Generation: Hydroelectric and thermal plants often use PCCP for efficient water transport.
Advantages of PCCP
PCCP offers a range of advantages that make it a preferred choice for large-scale infrastructure:
- Its exceptional lifespan, often exceeding 100 years with proper maintenance, reduces replacement costs.
- The pipe’s high strength allows it to handle significant internal pressures and external loads.
- Its outer mortar coating provides effective protection against corrosion and environmental damage.
- PCCP is cost-effective over its lifecycle, offering reduced maintenance and repair costs.
- Made from recyclable materials, PCCP aligns with sustainable construction practices.
Challenges and Limitations of PCCP
Despite its strengths, PCCP is not without challenges:
- Wire Breakage: Over time, prestressing wires can deteriorate, particularly if the outer coating is compromised.
- Complex Repairs: Due to its layered construction, repairing PCCP requires specialized techniques and can be costly.
- Heavy Installation Requirements: The size and weight of PCCP necessitate specialized equipment and experienced labor.
- Corrosion Risk: If the protective outer layer fails, the steel components become vulnerable to corrosion.
Inspection, Maintenance, and Repair Methods
To ensure longevity, PCCP must be regularly inspected and maintained. Common inspection techniques include electromagnetic testing to detect wire breaks, acoustic monitoring for real-time stress analysis, and robotic or CCTV inspections for internal assessments.
When repairs are needed, methods such as carbon fiber wrapping and steel banding are employed to reinforce the pipe without major excavation. For isolated damage, line stopping and bypassing allow for safe, localized repairs without interrupting service.
Compatibility with Other Pipe Materials
PCCP is highly adaptable and can be connected to other pipeline systems using specialized fittings and adapters. This makes it compatible with:
- HDPE (High-Density Polyethylene): Used for flexible connections.
- Ductile Iron: Ideal for high-pressure transitions.
- Steel Pipes: Ensures seamless integration into industrial systems.
Proper jointing techniques are crucial to maintaining system integrity and long-term performance.
Industry Standards and Regulatory Compliance
PCCP manufacturing and installation must adhere to strict industry standards:
- AWWA C301: Governs the manufacturing of PCCP.
- AWWA C304: Covers design requirements for PCCP applications.
- ASTM C76: Sets guidelines for concrete pressure pipe specifications.
These standards ensure that PCCP installations meet safety, durability, and performance requirements.
Innovations and Future Trends in PCCP
The future of PCCP includes exciting advancements:
- Smart Monitoring Systems: AI Embedded sensors offer real-time condition monitoring.
- Advanced Coatings: New materials enhance corrosion resistance.
- Hybrid Designs: Blending traditional and modern materials for improved performance.
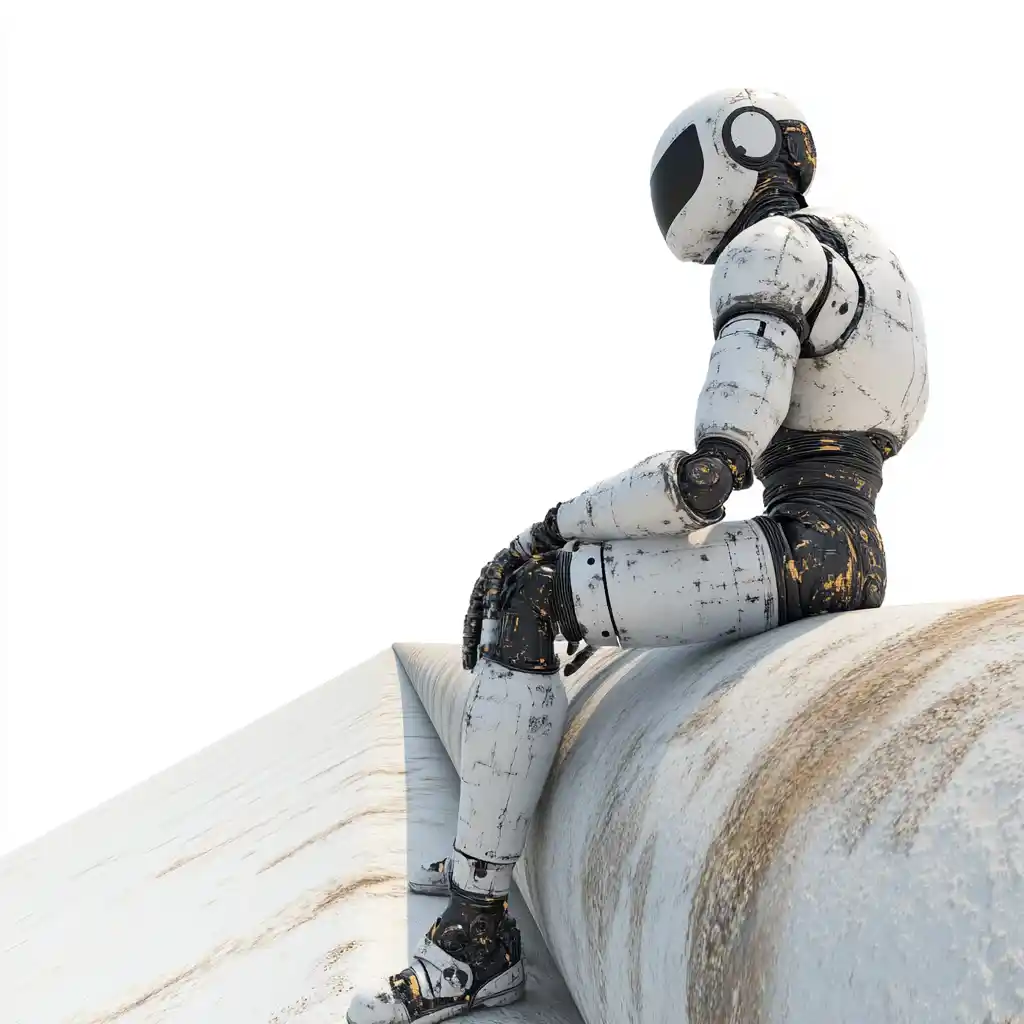
Do You Need Help With PCCP Services?
With over 20 years of experience, Watertap Inc. is a trusted leader in PCCP installation, inspection, and repair. Our team uses cutting-edge technology and proven industry practices to ensure efficient, safe, and reliable pipeline performance.
Contact us today to learn how Watertap Inc. can support your infrastructure needs.